Innovative and striking design is within your reach! Have you heard about the revolution in textile design? Say hello to 3D puff print. 3D puff print is a unique textile printing technique that adds a distinctive and tactile dimension to your designs. It’s not just print; it’s an art form that brings your creative ideas to life with an elevated, textured surface.
What is 3D puff print?
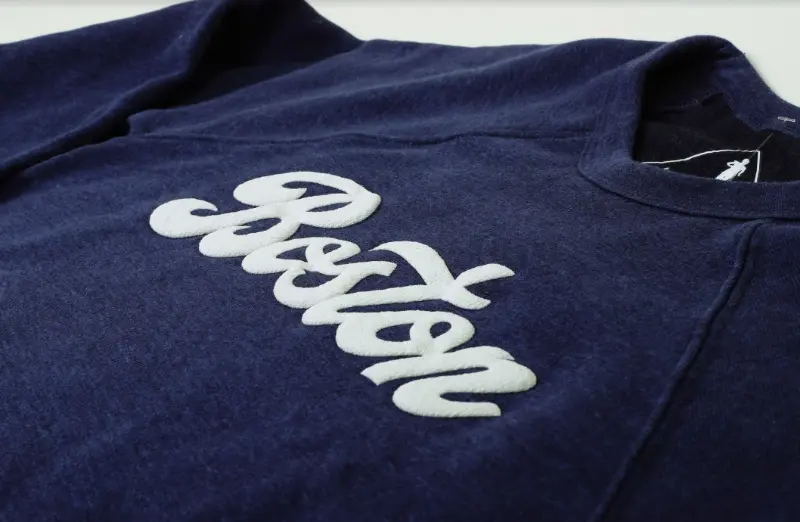
3D puff printing is a technique used in the field of custom apparel and textiles, particularly in the creation of embroidered designs on clothing items such as hats, jackets, and shirts. Unlike traditional flat embroidery, 3D puff printing adds a three-dimensional, raised effect to the design, giving it a textured and raised appearance.
The process involves using a special type of foam material that is placed on the fabric before the embroidery is done. The foam acts as a base for the stitches, allowing them to be raised above the fabric surface. When the embroidery is completed, the excess foam is trimmed away, leaving behind the raised and textured design.
This technique is often used to create bold and eye-catching designs that stand out on the fabric. It adds depth and dimension to the embroidery, making it a popular choice for logos, lettering, and other graphic elements on various types of apparel.
The 3D puff effect can be especially effective on items like baseball caps, where the raised design adds a tactile and visually interesting element to the garment.
3d Puff Print Avantages
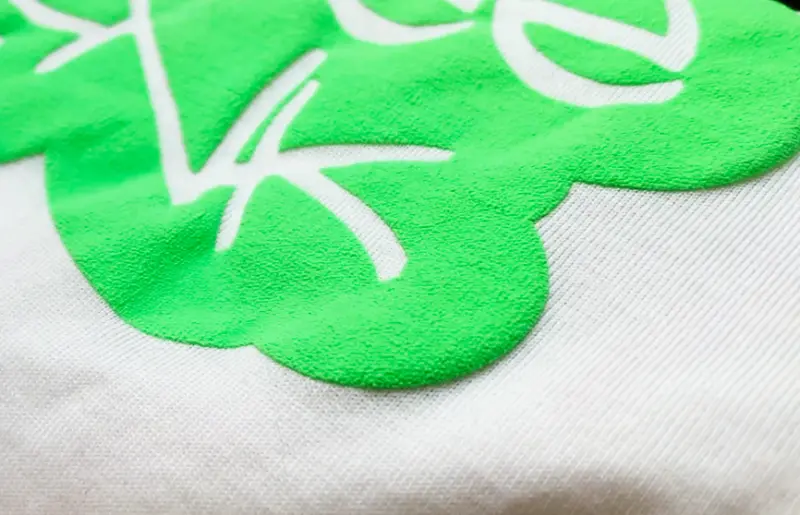
3D puff printing offers several advantages that make it a popular choice for adding texture and dimension to embroidered designs on apparel. Here are some of the key advantages:
- Textured and Raised Appearance: The primary advantage of 3D puff printing is its ability to create a three-dimensional and raised effect on the fabric. This adds texture and depth to the design, making it visually interesting and enhancing the overall look of the apparel.
- Enhanced Visibility: The raised nature of 3D puff prints makes them highly visible. This is particularly advantageous for logos, lettering, and other graphic elements that need to stand out and catch the viewer’s attention.
- Unique Aesthetic: The textured and raised appearance of 3D puff prints provides a unique and distinctive aesthetic. It allows for creative and eye-catching designs that may not be achievable with traditional flat embroidery.
- Versatility: 3D puff printing can be applied to a variety of fabrics, including hats, jackets, shirts, and other apparel items. This versatility makes it suitable for a wide range of products and design applications.
- Customization: The technique allows for customization of designs, making it possible to create intricate and personalized embroidered patterns with a three-dimensional effect.
- Branding Impact: Logos and brand elements created using 3D puff printing can have a more significant impact on branding efforts. The raised design adds a tactile quality that can contribute to brand recognition.
- Durable Finish: When done correctly, 3D puff prints can be durable and withstand regular wear and washing. This is important for ensuring that the textured design maintains its quality and appearance over time.
- Variety of Colors: 3D puff printing can be done in a variety of colors, allowing for creative and colorful designs. The technique works well with both single-color and multicolor designs.
- Popular for Headwear: The technique is particularly popular for headwear, such as baseball caps, where the raised design adds a unique and stylish element to the cap.
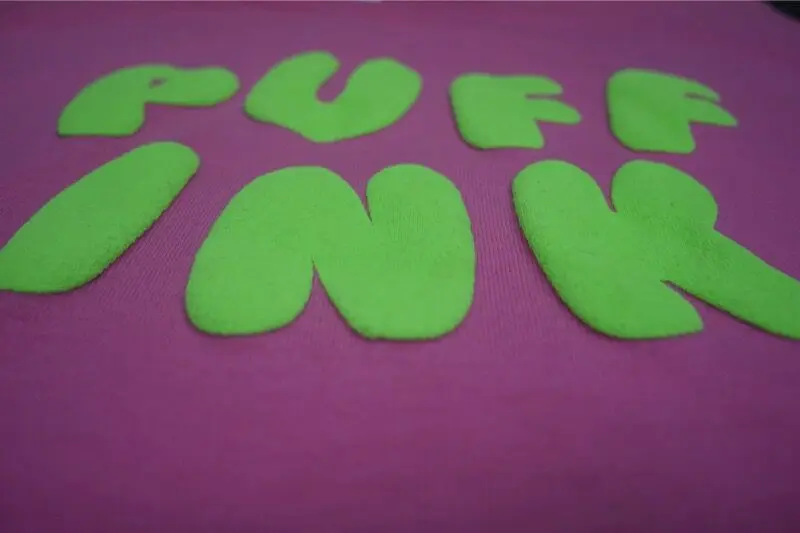
How To 3d Puff Print – Step By Step Guide
3D puff printing is a technique used in garment decoration, particularly in custom apparel such as hats and T-shirts, to add a three-dimensional effect to designs. The process involves using a special type of ink that puffs up when heated, creating a raised or textured surface. Here’s a step-by-step guide on how to perform 3D puff printing:
Materials and Tools
- Garment or Textile:
- Choose the item you want to print on, such as a hat, T-shirt, or hoodie.
- Screen Printing Frame and Mesh:
- Prepare a screen printing frame with mesh appropriate for your design.
- Emulsion and Scoop Coater:
- Coat the screen with emulsion using a scoop coater. Ensure an even and thin coat.
- Artwork and Film Positives:
- Create your design digitally and print it as a film positive. This will be used to transfer your design onto the screen.
- Exposure Unit:
- Expose the coated screen to UV light using an exposure unit. The film positive is placed on the screen, and the UV light hardens the emulsion, leaving your design on the screen.
- Water Source:
- Rinse the screen with water to wash away the unexposed emulsion, revealing your design on the screen.
- 3D Puff Printing Ink:
- Use a special 3D puff printing ink. This ink contains a puffing agent that expands when heated, creating the raised effect.
- Screen Printing Press:
- Set up your screen on a screen printing press. This press holds the screen steady and allows for precise placement on the garment.
- Flash Dryer or Heat Press:
- You’ll need a flash dryer or a heat press to cure the ink. The flash dryer uses hot air, while the heat press uses heat and pressure.
Steps
- Prepare Your Artwork:
- Design your artwork with the 3D puff effect in mind. Keep in mind that fine details may be lost in the puffing process.
- Coat the Screen:
- Apply emulsion to the screen using a scoop coater. Allow it to dry in a dark, cool area.
- Expose the Screen:
- Place your film positive on the coated screen and expose it to UV light. Follow the exposure time guidelines for your emulsion.
- Wash Out the Screen:
- Rinse the screen with water to wash out the unexposed emulsion. This will leave openings in the screen where the ink can pass through.
- Set Up the Press:
- Load the garment onto the screen printing press, ensuring it is secure and aligned.
- Apply the 3D Puff Ink:
- Using a squeegee, apply the 3D puff ink onto the garment through the screen. Ensure even coverage.
- Flash Cure:
- Use a flash dryer or heat press to partially cure the ink. This helps set the ink in place and prevents it from smearing when you lift the screen.
- Puff the Ink:
- After the flash cure, use a heat source to fully cure and puff the ink. The heat causes the puffing agent in the ink to expand, creating the raised effect.
- Cool and Inspect:
- Allow the garment to cool, and then inspect the print for quality. Ensure that the puffing is even and that the design meets your expectations.
- Final Cure:
- If necessary, do a final cure to ensure the ink is fully set and won’t wash out.
Keep in mind that the specifics of the process may vary based on the equipment and materials you are using. Always follow the manufacturer’s instructions for the particular products you have.
3d Puff Print Vs Regular Print
3D puff print and regular print depends on the specific requirements of the design, the desired visual effect, and the intended use of the printed item. Each method has its advantages and is suitable for different applications.
Feature | 3D Puff Print | Regular Print |
---|---|---|
Appearance | Raised, three-dimensional effect | Flat, two-dimensional surface |
Texture | Soft and tactile | Smooth and flat |
Material | Specialized puff ink or foam | Regular screen printing ink |
Printing Technique | Additional layer for puffiness | Direct application on fabric |
Ink Thickness | Thick and raised | Thin and flat |
Durability | Good, but may flatten over time | Generally durable |
Detail Level | Limited fine details | High level of detail possible |
Cost | Typically more expensive | Generally more cost-effective |
Versatility | Limited to certain designs/styles | Versatile for various designs |
Suitable Fabrics | Cotton and cotton blends | Various fabrics |
Ideal Use Cases | Bold and eye-catching designs | Standard or intricate designs |
Popular Applications | Logos, lettering, and simple designs | T-shirts, posters, apparel |
Production Time | Requires additional drying time | Faster production process |
Washability | Generally holds up well with washing | Durable, may fade over time |
How Do I Digitize 3d Puff Print?
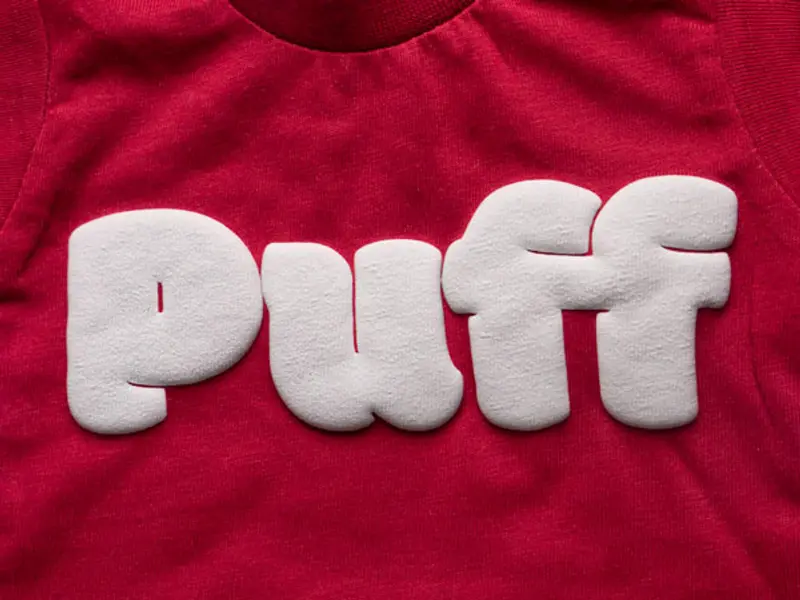
Digitizing a 3D puff print involves creating a digital file that represents the design in a format suitable for embroidery machines. Here are the general steps to digitize a 3D puff print:
- Create or Obtain the Design:
- If you’re creating the design from scratch, use graphic design software like Adobe Illustrator or CorelDRAW to design the logo or artwork.
- If you already have a design, ensure it’s in a digital format that can be imported into embroidery software.
- Choose Embroidery Software:
- Use specialized embroidery digitizing software such as Wilcom, Pulse, or Hatch to convert your design into a format compatible with embroidery machines.
- Open the Design in the Software:
- Import your design into the chosen embroidery software. The design should be a vector file for better scalability and quality.
- Set Embroidery Parameters:
- Define the size of your embroidery design and set other parameters such as stitch density, underlay stitching, and stitch type.
- Create the 3D Puff Effect:
- To achieve the 3D puff effect, you’ll need to add an underlay of stitches beneath the main design. This underlay raises the design off the fabric when stitched.
- Adjust Stitch Types:
- Modify the stitch types used in different areas of the design. For the 3D puff effect, you might use a combination of satin stitches, fill stitches, and special puff stitches.
- Specify Puff Foam Areas:
- Identify the areas where you want the 3D puff effect to appear. In these areas, the digitizing software will generate additional stitches to accommodate the puff foam.
- Specify Puff Foam Thickness:
- Indicate the thickness of the puff foam you plan to use. This helps the software calculate the necessary adjustments for the embroidery design.
- Preview the Design:
- Before finalizing the digitized file, preview the design in the software to check for any issues or areas that might need adjustment.
- Save the Digitized File:
- Once satisfied with the digitized design, save it in the appropriate file format supported by your embroidery machine (common formats include .DST, .EXP, .PES).
- Transfer to Embroidery Machine:
- Transfer the digitized file to your embroidery machine using a USB drive, card reader, or other compatible methods.
- Set Up Embroidery Machine:
- Load the chosen fabric into the embroidery machine, secure it properly, and set up the machine according to the digitized design’s requirements.
- Embroider the Design:
- Start the embroidery machine, and monitor the process to ensure that the 3D puff effect is being achieved as expected.
FAQs About 3d Puff Print
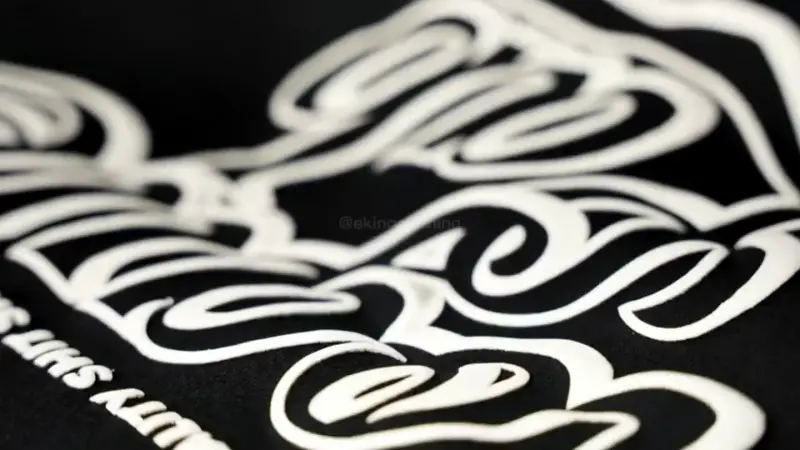
What Types Of Designs Work Best With 3d Puff Printing?
3D puff printing is best suited for simple and bold designs. Since the technique involves the expansion of foam to create the 3D effect, intricate details can be lost in the process. Hence, designs with large, blocky letters or simple iconic designs tend to work best.
Can 3d Puff Printing Be Used On Any Type Of Fabric?
While 3D puff printing can be used on a variety of fabrics, it works optimally on sturdy materials like denim, cotton, and polyester. Light, delicate fabrics may not withstand the heat and pressure applied during the process. Always consult with your printer to determine the best materials for your project.
How Does 3d Puff Printing Hold Up In The Wash?
3D puff prints are typically durable and can withstand regular washing. However, as with any special printing technique, it’s best to turn the garment inside out before washing, use cold water, and avoid the dryer to protect the design.
Is 3d Puff Printing More Expensive Than Traditional Printing Methods?
The cost of 3D puff printing can be slightly higher than traditional printing methods due to the additional materials (foam) and processing time. However, the unique, eye-catching effect it adds to the apparel often justifies the extra cost. Always check with your printer for a specific quote.
What is the difference between puff print and high density print?
Puff print and high-density print are two different techniques used in the field of textile printing, particularly in the production of custom apparel. Here’s a detailed table outlining the key differences between puff print and high-density print:
Feature | Puff Print | High-Density Print |
---|---|---|
Definition | A special type of screen printing that creates a raised, three-dimensional effect on the fabric. | A printing technique that results in a thick, textured layer of ink on the fabric, giving a raised and embossed appearance. |
Material Used | Puff additive or base, which expands when heated. | High-density additive or paste, often containing a thickening agent. |
Effect on Fabric | Creates a raised and puffy texture. | Produces a thick, embossed, and textured finish. |
Texture | Soft and spongy feel. | Firmer and more rigid feel due to the higher ink concentration. |
Appearance | 3D effect with a slightly rounded appearance. | Raised and embossed, often with sharper edges. |
Printing Process | Similar to regular screen printing but involves an additional layer of puff additive. | Similar to regular screen printing but with an additional layer of high-density ink. |
Heat Application | Requires heat to activate the puffing effect. | Requires heat to cure the high-density ink and create the raised texture. |
Color Options | Can be applied with a variety of colors. | Limited color options due to the thickness of the ink layers. |
Durability | Generally durable, but excessive washing may affect the puffiness over time. | Offers good durability, but excessive washing might lead to some fading or cracking. |
Common Applications | Popular for creating unique textures and adding a playful element to designs. | Used for creating bold and tactile designs, often for logos or text. |
Suitable Fabrics | Can be applied to a variety of fabrics, but works best on cotton. | Suitable for cotton and other fabrics, but may not be as effective on stretchy materials. |
Cost | Generally more affordable compared to high-density printing. | Can be more expensive due to the additional material and printing process involved. |
Conclusion
In conclusion, 3D puff print presents an innovative and creative approach to traditional printing techniques. Its capacity to add depth and texture to designs opens up a realm of possibilities for artists, fashion designers, and merchandisers alike. However, the process requires precision and expertise to yield high-quality results. Despite its challenges, the unique touch and aesthetic appeal of 3D puff print make it a valuable addition to the world of print design.