In the dynamic world of textile and graphic printing, Simulated Process Screen Printing has emerged as a compelling technique that offers unmatched versatility and quality. This intricate method allows for the exquisite reproduction of designs with high color detail and gradients, making it the go-to choice for complex graphics.
In this informative post, we will delve into the nuances of Simulated Process Screen Printing, shedding light on its tips and techniques that can elevate your printing game to a whole new level. Stay with us as we unravel the art of this unique printing process.
What Is Simulated Process Printing?
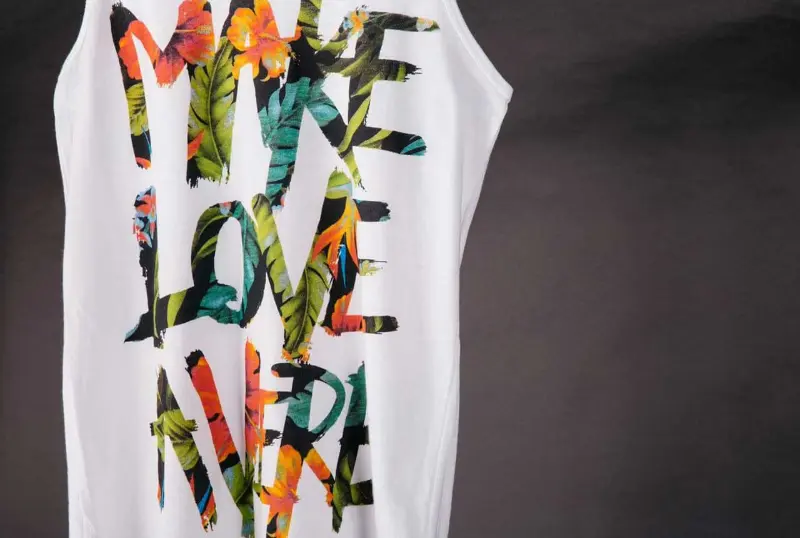
Simulated Process Printing is a method of printing photorealistic images on dark or colored garments using halftone dots of many colors.
Unlike traditional screen printing, which uses large, solid areas of color, this technique employs halftones of a few ink colors to represent the colors in the original artwork. A screen is prepared for each color, and the screens are then printed in layers to create an image that mimics the look of the original.
The main advantage of simulated process printing is its ability to reproduce complex, multicolored designs with a high level of detail and smooth color transitions. It also allows for the use of more colors than traditional screen printing methods, making it an ideal choice for designs with a wide color range or those that require photographic realism.
Despite its complexity, this printing technique has gained popularity due to its versatility and the high-quality results it produces.
Pros
- Color Accuracy: Simulated process printing can achieve high color accuracy, allowing for the reproduction of complex and vibrant images.
- Wide Color Gamut: It enables the printing of a wide range of colors and gradients using a limited set of spot colors, providing a more extensive color gamut compared to some other printing methods.
- Versatility: This technique is suitable for a variety of substrates, including textiles, paper, and other materials, making it versatile for different applications.
- Cost-Effective: Simulated process printing can be more cost-effective than traditional four-color process printing because it often requires fewer screens and ink colors.
- Detail Reproduction: It excels at reproducing fine details in images, making it suitable for intricate and detailed designs.
- Suitable for Dark Substrates: Simulated process printing is effective on dark-colored substrates, where traditional four-color process printing may not be as vibrant.
Cons
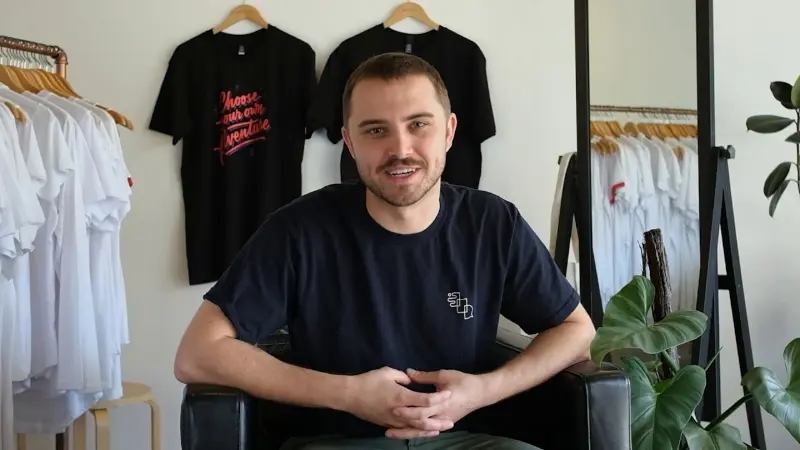
- Complex Setup: The setup for simulated process printing can be more complex and time-consuming compared to simpler printing methods, especially for those new to the technique.
- Skill and Experience Required: Achieving optimal results with simulated process printing requires a certain level of skill and experience, particularly in color separation and ink mixing.
- Limited Color Matching: While simulated process printing can reproduce a wide range of colors, there may be limitations in matching specific colors accurately, especially when dealing with corporate branding or exact color requirements.
- Ink Mixing Challenges: Achieving consistent and accurate ink colors can be challenging, and variations in ink batches may occur, affecting color consistency across prints.
- Screen Alignment and Registration: Maintaining precise screen alignment and registration throughout the printing process is crucial. Any misalignment can result in color shifts and a less accurate final print.
- Cost of Inks: The cost of specialized inks for simulated process printing can be higher compared to standard inks used in simpler printing methods.
Is Simulated Process Printing More Expensive?
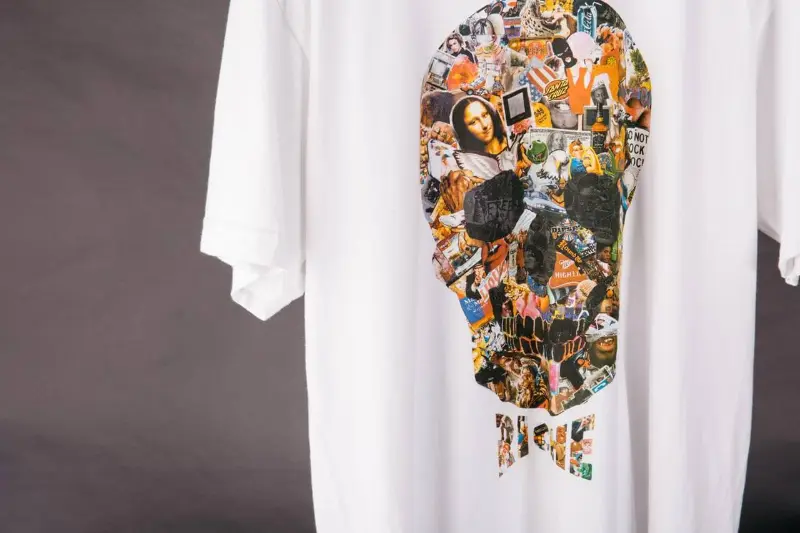
More Color Separations
Simulated process printing, often referred to as SIM process, is a technique that blends and overlays primary and secondary colors to replicate a full color spectrum. It’s a common choice for complex designs or designs that require a high level of detail.
However, one of the factors that can contribute to the cost of SIM process printing is the necessity for more color separations.
Color separations are the different individual color components that make up a printed image. Each separation corresponds to a different screen used in the printing process, so each additional separation adds to the complexity of the operation.
The number of color separations in a print job directly affects the cost of the job because each separation requires its own screen, ink mix, and press setup time.
When it comes to SIM process printing, the technique often requires a greater number of color separations compared to traditional screen printing methods. This is because SIM process printing uses halftones of each ink color to create a wider range of colors and more subtle gradations in the final image. As a result, designs that use SIM process printing can end up being noticeably more expensive due to the higher number of color separations required.
Furthermore, the increased number of color separations also entails longer setup and clean up times, which in turn, adds to labor costs. This additional time is necessary to prepare each color separation and to clean the equipment between each run. Therefore, the overall expense associated with SIM process printing, especially in terms of labor, can be quite significant.
Spot Color Inks
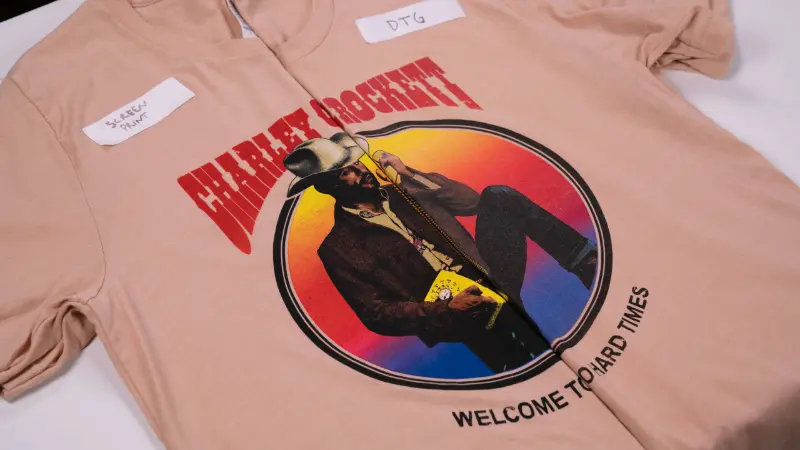
When discussing cost comparison between simulated process printing and spot color inks, several factors come into play. Simulated process printing, a method that uses halftone dots of few colors to represent the colors in the original image, can be more expensive due to the intricacy of the process. The process requires a high level of expertise and precision, hence leading to a higher labor cost.
Moreover, the complexity of simulated process printing may also contribute to a longer setup time, which can add to the cost. Unlike spot color printing which uses separate plates for each color, simulated process printing requires careful alignment of the different color halftones. Misalignment can lead to a distorted final print, making precision crucial.
On the other hand, spot color inks have their own set of expenses. These inks are custom-mixed for each job, a process that can be laborious and time-consuming. Furthermore, the use of spot colors may increase the number of colors required for a print job, thereby increasing the cost of inks.
However, it’s essential to note that the cost can also be influenced by the quantity of the print run. For large quantities, the cost per unit for simulated process printing might decrease, making it comparably priced to spot color inks.
Color Matching And Adjustments
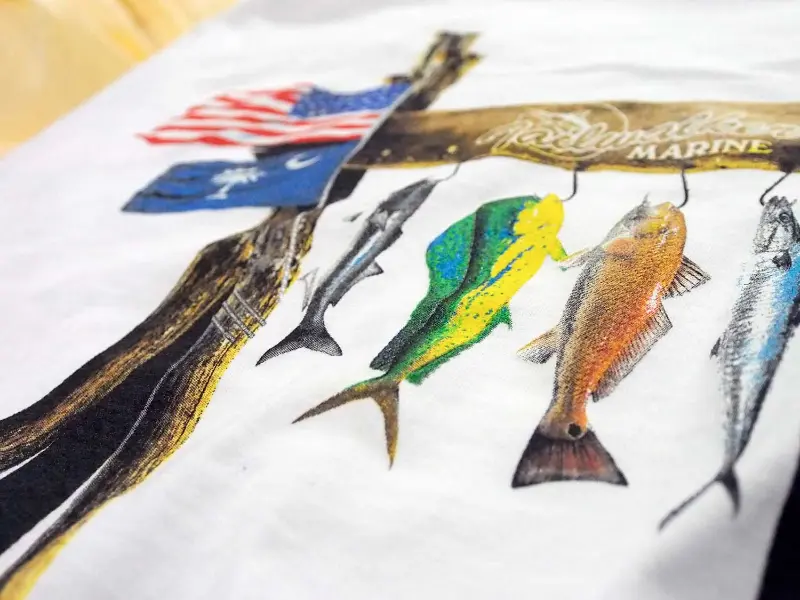
Simulated process printing, a complex technique involving the breakdown of an image into color components, can be more expensive than traditional spot color printing. This advanced process requires specialized software and an adept hand at color separation, which can drive up costs.
The price can further escalate depending on the number of colors involved, as each color needs a separate screen, increasing both material and labor costs.
The color matching process in simulated process printing is intricate, demanding a high degree of precision to achieve the desired result. Adjustments must be made to ensure each color layer accurately contributes to the final image. This can be a time-consuming process as it involves a lot of trial and error, leading to higher costs.
Yet, the higher price point of simulated process printing can be justified by the superior quality of print it offers. It allows for a greater range of colors and smoother gradients, resulting in a more refined and photorealistic image. For designs with high levels of detail or a broad color spectrum, simulated process printing may be the only viable option.
However, it’s worth noting that the cost-effectiveness of simulated process printing can improve when used for larger print runs. The upfront costs for setup are relatively high, but once the screens are created, the actual printing cost per unit can be significantly less. This makes it a more economical choice for larger orders.
In conclusion, while simulated process printing is often more expensive due to the complexity of the process and the level of skill required, the resulting print quality can justify the expense. Budget, design complexity, and the volume of the print run are essential variables to consider when deciding between simulated process printing and other printing methods.
Expertise And Setup
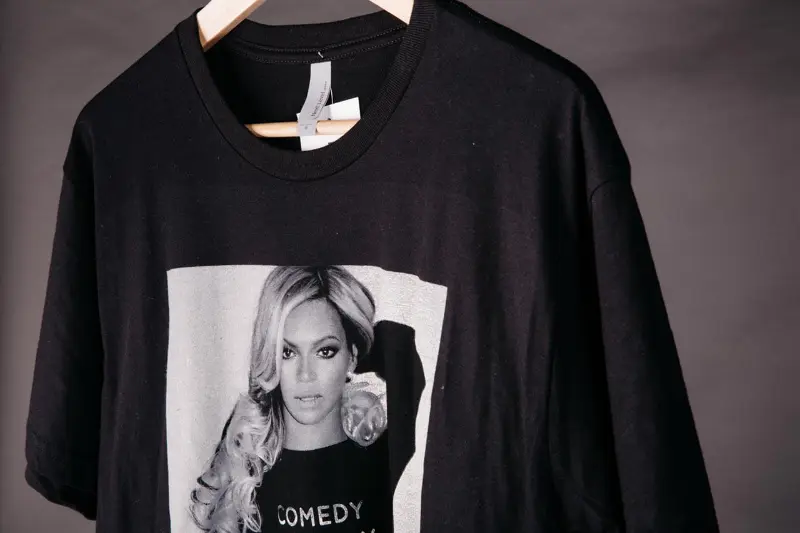
Simulated Process Printing, although renowned for its ability to reproduce complex images with a wide color spectrum on dark fabrics, is often perceived as a more expensive printing method. This perception is largely due to the expertise required and the setup process involved.
The expertise needed for Simulated Process Printing is significantly higher when compared to other printing methods. It requires an experienced and skilled printer to manipulate the colors accurately, ensuring each ink layer is correctly aligned to create the stunning and detailed final product. The cost of employing such skilled labor can indeed drive up the overall cost.
The setup process for Simulated Process Printing is also more involved and complex. Each color used in the design needs its own screen, and setting up these screens can be time-consuming. Moreover, the ink used in this process is specific and often more expensive than traditional inks. The combination of the costlier ink and the time taken for the setup process contribute to making Simulated Process Printing a pricier option.
Nevertheless, it’s important to consider the quality and details that Simulated Process Printing can achieve, which are unparalleled by most other methods. When comparing the costs, one must take into account the end result. For intricate designs requiring a high level of detail and a wide color range, Simulated Process Printing could be a value-for-money option despite its higher upfront costs.
To sum up, while Simulated Process Printing may seem more expensive due to the expertise needed and the complex setup process, the superior quality it produces can justify the costs involved, especially for intricate, colorful designs. Thus, the decision to choose this over other printing methods should be guided not only by the cost but also by the desired outcome.
key steps involved in simulated process screen printing
Simulated process screen printing is a technique used in the screen printing industry to reproduce full-color images with a limited number of ink colors. Unlike traditional four-color process printing, which uses the CMYK color model, simulated process screen printing uses a set of specially mixed spot colors to achieve a wide range of colors and gradients.
Here are the key steps involved in simulated process screen printing:
Step1: Color Separation
The first step is to separate the full-color image into a set of spot colors. This is typically done using image editing software like Adobe Photoshop. Each color in the design is separated into a different channel, and specific ink colors are assigned to each channel.
Step 2: Halftone Screens
Each color separation is converted into a halftone screen. Halftones use dots of varying sizes to simulate different tones and colors. The size and spacing of the dots determine the perceived color and intensity. This process is crucial for creating the illusion of continuous tones with a limited color palette.
Step 3: Printing Screens
Separate screens are created for each color using the halftone screens. These screens are coated with a light-sensitive emulsion, and the color separations are exposed onto each screen using a light source. After exposure, the screens are washed, revealing the stencil of the design on each screen.
Step 4: Printing Setup
The screens are mounted onto the printing press in registration, ensuring that each color lines up accurately with the others. Registration marks are used to align the screens precisely.
Step 5: Ink Mixing
Specially formulated inks are mixed to match the desired colors in the design. The printer needs to carefully match the ink colors to the specified Pantone or custom color values.
Step 6: Test Printing
Before the actual production run, a few test prints are usually done to check color accuracy, registration, and overall print quality. Adjustments may be made to the screens, ink formulations, or printing parameters based on the test prints.
Step 7: Production Printing
Once everything is set up and confirmed, the full production run can begin. The printer applies each color of ink through its respective screen, building up the complete image.
FAQs About Simulated Process Screen Printing
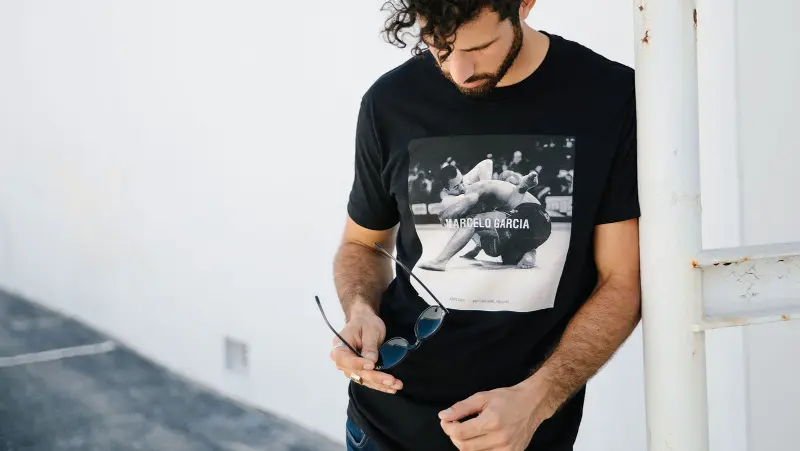
What Is Simulated Process Screen Printing?
Simulated Process Screen Printing is a complex method of screen printing that uses the process of color separation to produce highly detailed and colorful prints. Unlike traditional screen printing which utilizes spot colors, this method breaks down the image into several color components or halftones.
Each color is then screen printed one at a time to recreate the original image with a high level of detail and a wide color spectrum. It is a preferred method for printing complex and multi-colored designs, especially on dark garments.
How Does Simulated Process Screen Printing Differ From Other Printing Methods?
Unlike other printing methods, Simulated Process Screen Printing allows for greater color depth and detail in the final print. Traditional screen printing methods are limited by the number of colors that can be used, typically resorting to block colors or simple designs.
However, simulated process screen printing can achieve photorealistic results by separating colors into halftones and layering them onto the product. This method also allows for printing on dark fabrics without requiring a base layer, which is a common requirement in traditional screen printing.
What Are The Advantages Of Using Simulated Process Screen Printing?
The main advantage of Simulated Process Screen Printing is its ability to print complex, multi-colored, and photorealistic designs on various substrates, including textiles and promotional products. Its precision in color separation and layering allows for a wide color gamut and greater detail in the final print.
Moreover, since it does not require a white underbase for printing on dark garments, the final prints feel softer to the touch compared to other methods.
Conclusion
In conclusion, Simulated Process Screen Printing stands out as a remarkable technique in the printing industry due to its capability to deliver intricate, multi-colored, and photorealistic designs. Its unique approach of color separation and layering offers a broad color range and exceptional detail in the final product, even on dark fabrics.
This technique, while complex, reaps results that are not only visually appealing but also durable, maintaining their vibrancy even after repeated washing. Thus, for those seeking high-quality prints with a soft touch and long-lasting appeal, Simulated Process Screen Printing is an excellent choice.